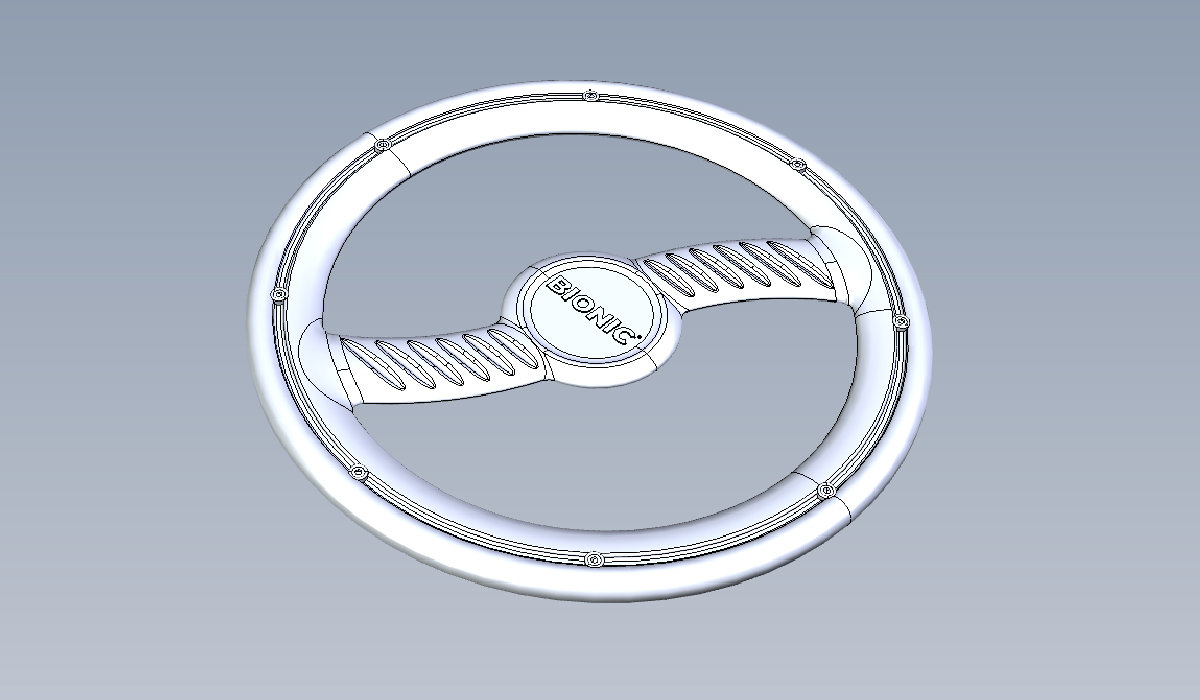
Developing durable dog toys that can withstand the enthusiasm and energy of heavy chewers is challenging. There are many components in developing BIONIC® dog toys and innovative technologies for making injection steel molds are some of them. Our state-of-the-art steel molds are one of the secrets behind the durability and longevity of BIONIC dog toys. Let’s wag into the fascinating world of injection mold tools and explore how the design and fabrication of BIONIC’s molds help provide Tail Wagging Durability for your dog.
The Art of Injection Molding
Injection molding is a manufacturing process that involves injecting molten BIONIC RUBBER® into a steel mold cavity. The molds used in the production of BIONIC dog toys allow for the creation of intricate details and textures that add to BIONIC function and durability. Whether it’s the nub channels or compartments for treats, BIONIC design elements provide a sensory experience that stimulates your dog’s natural instincts and keeps them engaged, together with forms that provide durability.
The use of high-quality steel molds ensures that every detail of BIONIC toy designs are captured with utmost precision. From the intricate patterns to the texture and shape, BIONIC steel molds guarantee that each toy is an exact replica of our original design. This level of accuracy is crucial for creating BIONIC toys that are not only durable but also safe and enjoyable for your dog.
The Power of Injection Steel Molds
Once the design phase of a new BIONIC dog toy is complete, we then create a detailed design of the steel mold tool to be fabricated. This includes developing the dimensions, features, and specifications of the steel mold, based on the BIONIC toy design to be manufactured.
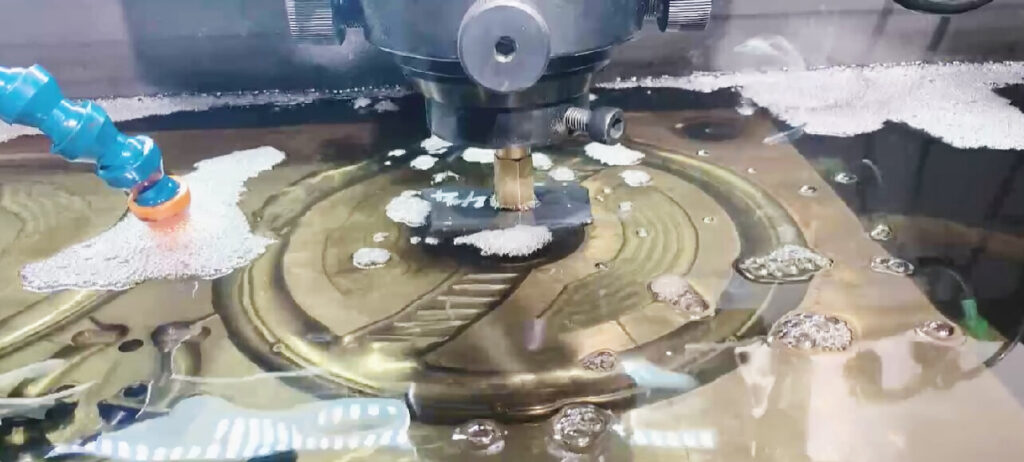
The BIONIC mold tool is then fabricated with CNC (Computer Numerical Control) machines and other precision machining techniques to shape a steel block into a BIONIC toy shaped mold cavity. This process involves milling, turning, drilling, and grinding operations to create the necessary features, such as cavities, cores, and venting channels of the BIOINC mold.
After machining the BIONIC mold, it undergoes a heat treatment process to enhance its hardness and durability. This step involves heating the mold to a specific temperature and then cooling it at a controlled rate.
Polishing the surfaces of the mold cavity is then preformed to achieve the desired smoothness and texture. This helps ensure that BIONIC dog toys produced from the mold have the desired surface characteristics.
The BIONIC mold tool is then assembled by attaching the mold halves together, incorporating necessary mechanisms like ejector pins, cooling channels, and alignment features. Once assembled the mold goes through testing and cycle trials to ensure proper functionality and the ability to produce high-quality BIONIC products.
After passing the testing phase, the tool can be used for mass production of BIONIC products using a large injection molding machine. Engineers clamp the mold tool to the injection machine and molten BIONIC RUBBER is injected into the mold cavity under high pressure. After cooling and solidifying, the mold is opened and automatically ejects out a BIONIC dog toy.
The combination of high-quality steel molds, BIONIC RUBBER, meticulous toy design, and rigorous quality control ensures that BIONIC toys developed by teams of dog loving designers and engineers will last and keep tails wagging.